How to Choose the Right Industrial Scale for Your Business Needs
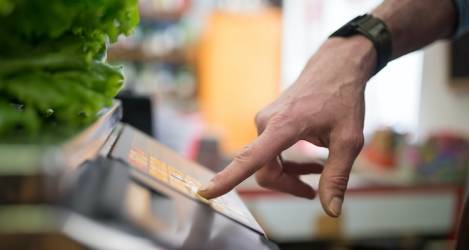
The weight of goods and materials might seem straightforward, but it's a cornerstone of business operations across numerous industries. From logistics and manufacturing to food and pharmaceuticals, the ability to accurately and efficiently measure weight can have far-reaching implications for profitability, regulation compliance, and customer satisfaction. But with many industrial scale options on the market, how do you pick the scale that perfectly aligns with your business requirements?
Assess Capacity and Precision Needs
The first step in selecting the right scale is evaluating your specific capacity and precision needs. For businesses that deal with heavy loads, the Ohaus Defender series offers robust performance with its high weight capacity and durable construction, making it an ideal choice for industrial environments. It is essential to ensure the scale you select can handle the maximum weights you plan to measure, but just as crucial is the scale's precision, especially in industries where accuracy is paramount.
A scale that offers precision measuring ensures you meet strict compliance standards and avoid costly errors in weight-based transactions. Furthermore, the Defender's level of precision makes it suitable for tasks that require meticulous weight measurements, such as formulating mixtures or portioning out products. By thoroughly assessing your operations' weight and precision needs, you will be on solid ground to choose a scale that can streamline your processes and enhance business efficiency.
Consider the Environment
The environmental conditions where the scale will be used greatly impact the choice of scale. In dusty, debris-filled, or wet environments like construction sites or food processing plants, scales such as the Mettler Toledo PBA430 are built to endure harsh conditions, maintaining accuracy and durability. In cleaner, controlled settings like labs or pharmaceutical manufacturing, Adam Equipment Nimbus precision scales provide precise measurements in a delicate environment.
When assessing the environment, consider temperature changes and potential chemical exposures. This may require a scale with protective coatings. Ease of cleaning is essential; stainless steel scales are preferred for their durability and cleanliness. Choosing a scale that meets environmental needs ensures accurate and reliable performance.
Evaluate the Scale's Features
In addition to capacity and environmental suitability, it's equally essential to scrutinize a scale's features. Modern scales come equipped with advanced functionalities like wireless connectivity, allowing for seamless integration with inventory management systems and facilitating real-time data tracking. User-friendly interfaces and display readability are also essential for efficient operation, minimizing errors and training time for staff.
Safety features, such as overload protection, ensure the longevity of the scale and protect operators. Additionally, a scale with a modular design may offer the convenience of being easily upgradable, catering to your business's evolving demands. Therefore, a comprehensive evaluation of these features will contribute significantly to selecting an industrial scale that meets current and future needs.
Regulation Compliance
Ensuring adherence to local and international regulations is critical to choosing an industrial scale. Businesses must be aware of the various standards and certifications that pertain to their industry, such as the International Organization of Legal Metrology (OIML) or the National Conference on Weights and Measures (NCWM). A pre-calibrated scale and certification of these standards can vastly simplify compliance processes.
Additionally, consider scales that feature tamper-proof seals or software that maintains a calibration and measurement data record, enhancing traceability and accountability. By looking for accreditation labels and audit capabilities on a scale, you will significantly reduce the risk of non-compliance penalties. In sum, regulatory conformity should be a pivotal factor in the purchasing decision on an industrial scale.
User Interface and Ease of Use
Considering usability and user interface is crucial for an industrial scale. An intuitive, easy-to-operate scale reduces employee training time and errors. Features like touchscreen displays, customizable settings, and user-friendly manuals are key. For instance, scales such as the Rice Lake SURVIVOR PT Series offer a simple touchscreen interface and a comprehensive help menu for effortless operation.
Furthermore, consider the scale's compatibility with other equipment and software used in your business operations. An integrated system will streamline data sharing and increase overall efficiency. Ultimately, choosing a scale with a user-friendly interface and seamless integration capabilities can significantly impact your business's productivity and success.
Maintenance and Support
Once you have chosen and installed an industrial scale, it's crucial to consider the maintenance and support services available. Scales are intricate devices that require regular calibration and upkeep to ensure accuracy and longevity. Look for manufacturers or distributors that offer maintenance plans, repair services, and readily available spare parts in case of a breakdown.
Furthermore, ensure that the manufacturer provides prompt technical support in case of any issues or questions. By proactively addressing maintenance needs, you can avoid costly downtime and ensure your scale continues to support your business operations effectively.
Choosing the correct industrial scale is crucial. Assess your business needs, consider environment and compliance standards, evaluate features and usability, and ensure maintenance and support. This informed decision benefits your operations. The scale is more than a weight tool; it invests in efficiency, safety, and precision. Evaluate options wisely for long-term success.